Fasteners play a crucial role in engineering and manufacturing. DIN and ANSI standard fasteners provide technical guidelines to ensure their quality, compatibility, and safety. DIN standards originate from the German Institute for Standardization, while ANSI standards come from the American National Standards Institute. These standards hold significant importance in both regional and global industries. They help you achieve uniformity and reliability when selecting DIN and ANSI standard fasteners for various applications. Understanding these standards allows you to make informed decisions and maintain consistency in your projects.
Key Takeaways
- DIN and ANSI standards ensure fasteners meet strict quality, safety, and compatibility requirements, enhancing project reliability.
- Understanding the differences between DIN (metric) and ANSI (imperial) standards helps you select the right fasteners based on your project’s location.
- Both DIN and ANSI standards provide precise dimensions and material specifications, reducing the risk of mismatched components.
- Adhering to these standards simplifies the selection process and ensures that fasteners perform well under various conditions.
- Using standardized fasteners fosters global trade by allowing components from different manufacturers to work seamlessly together.
- By following DIN and ANSI guidelines, you contribute to a more efficient supply chain and enhance the safety of your projects.
- Knowledge of these standards empowers you to make informed decisions, ultimately leading to greater success in engineering, manufacturing, and construction.
Understanding DIN Fastener Standards
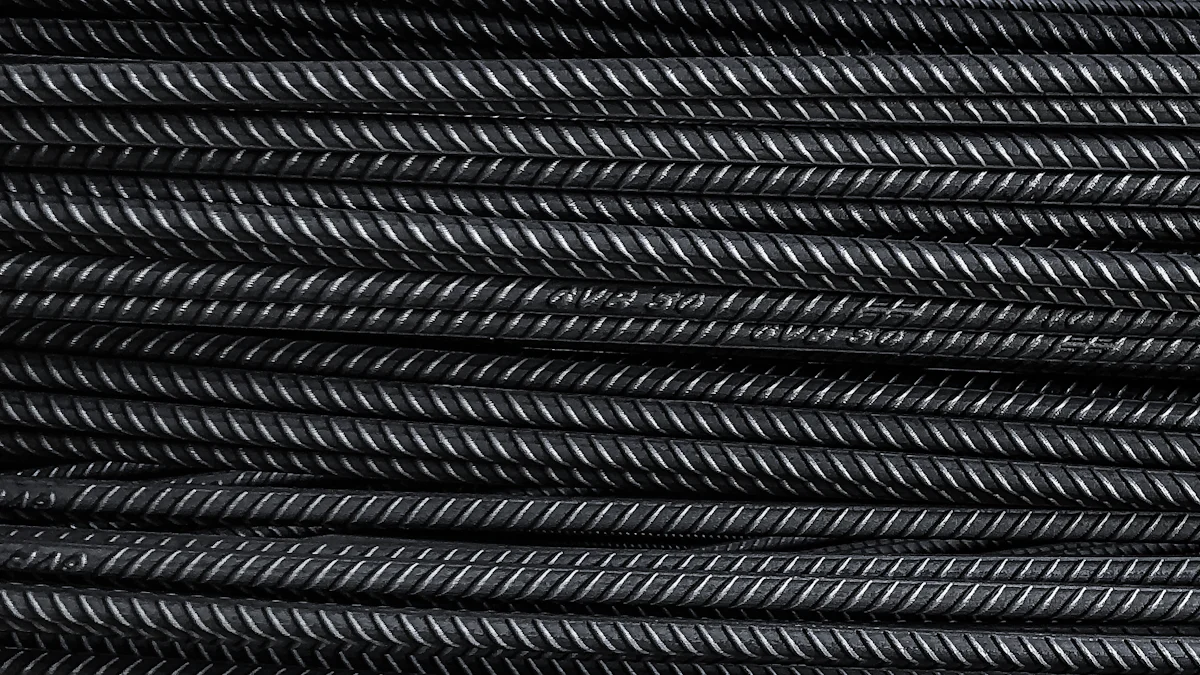
Origin and Purpose of DIN Standards
DIN standards, established by the German Institute for Standardization, have a long history of promoting precision and reliability. These standards originated in Germany to create uniform guidelines for manufacturing and engineering. You can trace their roots back to 1917 when the institute was founded to address the need for consistent industrial practices. Over time, DIN standards expanded to cover a wide range of industries, including fasteners.
The primary purpose of DIN standards is to ensure consistency in product dimensions, materials, and performance. By following these standards, you can achieve compatibility between components, even when sourced from different manufacturers. This consistency reduces errors and enhances the efficiency of your projects. DIN standards also prioritize safety, ensuring that fasteners meet strict quality requirements for various applications.
Key Features of DIN Fastener Standards
DIN fastener standards focus on several critical aspects to maintain quality and reliability. First, they define precise dimensions for fasteners, such as screws, bolts, and nuts. These specifications help you select the right fastener for your project without worrying about mismatched parts. The standards also outline material requirements, ensuring that fasteners can withstand specific loads and environmental conditions.
Another key feature is the inclusion of testing methods. DIN standards provide detailed guidelines for evaluating fastener strength, durability, and performance. By adhering to these methods, you can verify that the fasteners meet the necessary criteria for your application. Additionally, DIN standards emphasize ease of use. They simplify the selection process by categorizing fasteners based on their intended purpose and characteristics.
DIN and ANSI standard fasteners share some similarities, but DIN fasteners often use metric measurements. This distinction makes them particularly suitable for projects in regions where the metric system is standard. Understanding these features allows you to make informed decisions and ensures that your fasteners meet the demands of your work.
Understanding ANSI Fastener Standards
Origin and Purpose of ANSI Standards
ANSI standards, developed by the American National Standards Institute, play a vital role in ensuring consistency and safety in fastener applications. ANSI began its work in 1918 to create unified guidelines for industries across the United States. Over the years, it has become a trusted authority for standardization in engineering, manufacturing, and construction.
The primary goal of ANSI standards is to establish uniformity in fastener dimensions, materials, and performance. By following these standards, you can ensure that fasteners from different manufacturers work seamlessly together. This compatibility reduces errors and simplifies your project planning. ANSI standards also focus on safety by requiring fasteners to meet strict quality benchmarks. These guidelines help you select reliable fasteners for demanding applications, ensuring durability and performance.
Key Features of ANSI Fastener Standards
ANSI fastener standards emphasize precision and practicality. They define exact measurements for fasteners, including screws, bolts, and nuts, using the imperial system. This focus on standard dimensions ensures that you can easily find fasteners that fit your specific needs. The standards also specify material requirements, helping you choose fasteners that can handle various loads and environmental conditions.
Testing methods form another critical aspect of ANSI standards. These guidelines provide clear instructions for assessing fastener strength, durability, and performance. By using these methods, you can verify that your fasteners meet the necessary criteria for your projects. ANSI standards also categorize fasteners based on their intended use, simplifying the selection process for you.
While DIN and ANSI standard fasteners share some similarities, ANSI fasteners cater primarily to industries in the United States. Their reliance on the imperial measurement system makes them ideal for projects in regions where this system is standard. Understanding these features allows you to make informed decisions and ensures that your fasteners meet the demands of your work.
Comparing DIN and ANSI Standard Fasteners
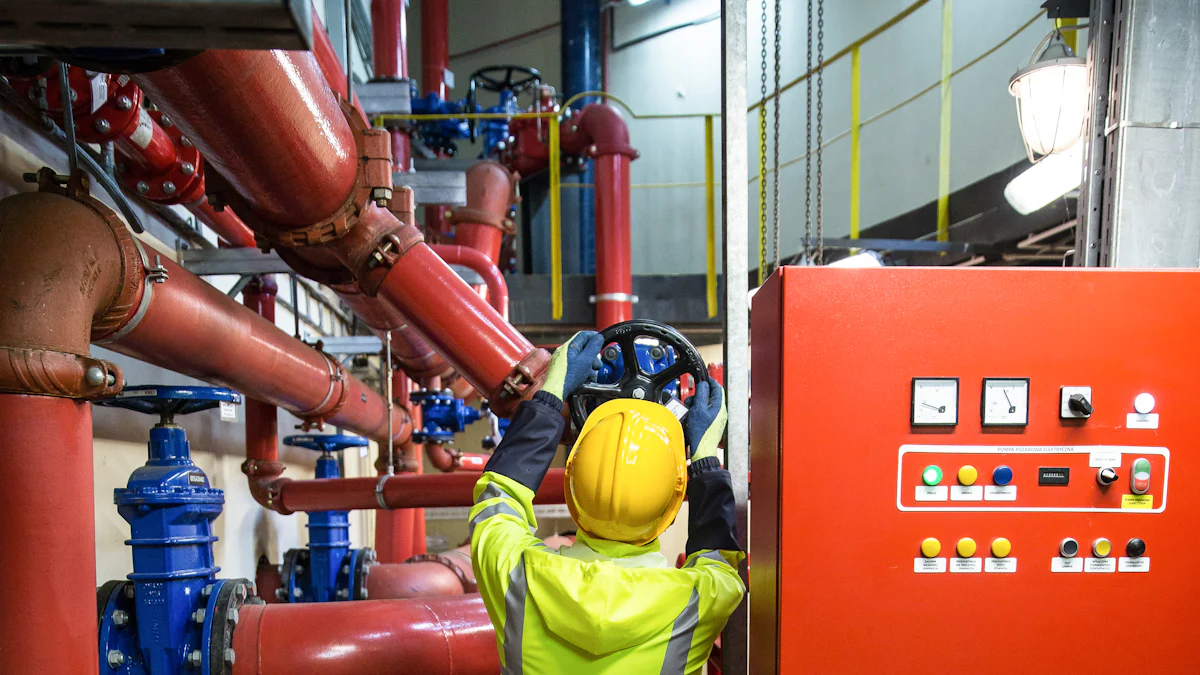
Key Differences Between DIN and ANSI Standards
DIN and ANSI standards differ in several key aspects. The most noticeable difference lies in their measurement systems. DIN standards primarily use the metric system, which is common in Europe and many other parts of the world. ANSI standards, on the other hand, rely on the imperial system, making them more suitable for industries in the United States. This distinction affects how you select fasteners based on your project’s location and requirements.
Another significant difference involves their regional focus. DIN standards originated in Germany and have a strong presence in European markets. ANSI standards, developed in the United States, cater to industries within the country. While both standards have global recognition, their primary applications often align with their regions of origin.
The scope of standardization also varies. DIN standards cover a broader range of industries and applications, including fasteners, machinery, and construction materials. ANSI standards focus more on specific industries, such as engineering and manufacturing. This difference means you may find DIN standards more versatile for diverse projects, while ANSI standards provide targeted solutions for particular needs.
Similarities Between DIN and ANSI Standards
Despite their differences, DIN and ANSI standards share several similarities. Both aim to ensure quality, safety, and compatibility in fasteners. By following these standards, you can trust that the fasteners meet strict guidelines for performance and reliability. This consistency reduces the risk of errors and enhances the efficiency of your projects.
Both standards emphasize precise dimensions and material requirements. They provide detailed specifications for fasteners, such as screws, bolts, and nuts. These guidelines help you select components that fit seamlessly into your designs. Additionally, both standards include testing methods to verify the strength and durability of fasteners. This focus on testing ensures that the fasteners perform well under various conditions.
Another similarity lies in their role in supporting global trade. DIN and ANSI standard fasteners enable manufacturers and engineers to work with components from different suppliers without compatibility issues. This uniformity fosters collaboration across industries and regions, making it easier for you to source reliable fasteners for your projects.
The Significance of DIN and ANSI Standard Fasteners
Ensuring Quality, Safety, and Compatibility
You rely on fasteners to hold your projects together, whether in construction, manufacturing, or engineering. DIN and ANSI standard fasteners ensure that these components meet strict quality benchmarks. These standards define precise dimensions and material requirements, helping you avoid mismatched or subpar fasteners. By using fasteners that adhere to these guidelines, you can trust their performance under various conditions.
Safety is another critical aspect. Fasteners that meet DIN and ANSI standards undergo rigorous testing to verify their strength and durability. This ensures they can handle the loads and stresses of your application without failure. When you use these fasteners, you reduce the risk of accidents caused by faulty components. Compatibility also becomes seamless. Standardized fasteners fit perfectly with other components, even when sourced from different manufacturers. This consistency simplifies your work and minimizes errors.
Supporting Global Trade and Industry Applications
In today’s interconnected world, industries depend on global trade to source materials and components. DIN and ANSI standard fasteners play a vital role in this process. Their standardized specifications allow manufacturers from different regions to produce fasteners that work together. This uniformity eliminates compatibility issues, making it easier for you to source reliable fasteners from international suppliers.
These standards also support a wide range of industry applications. Whether you work in automotive, aerospace, or construction, you can find fasteners that meet the specific demands of your field. DIN standards, with their metric measurements, are widely used in Europe and other regions. ANSI standards, based on the imperial system, cater to industries in the United States. This versatility ensures that you can select the right fasteners for your projects, no matter where you operate.
By adhering to these standards, you contribute to a more efficient and reliable global supply chain. You also gain access to high-quality fasteners that enhance the safety and performance of your work. Understanding the significance of DIN and ANSI standard fasteners helps you make informed decisions and ensures the success of your projects.
DIN and ANSI fastener standards provide clear guidelines to ensure fasteners meet specific quality, safety, and compatibility requirements. You can rely on these standards to select components that perform consistently and reduce risks in your projects. Understanding their purposes helps you make informed decisions, whether you work in engineering, manufacturing, or construction. By applying this knowledge, you enhance the reliability of your work and contribute to industry-wide efficiency. These standards are not just technical rules; they are essential tools for achieving precision and success in your field.
Post time: Nov-25-2024